Core Technology
Typical treatment processes for high-salt wastewater
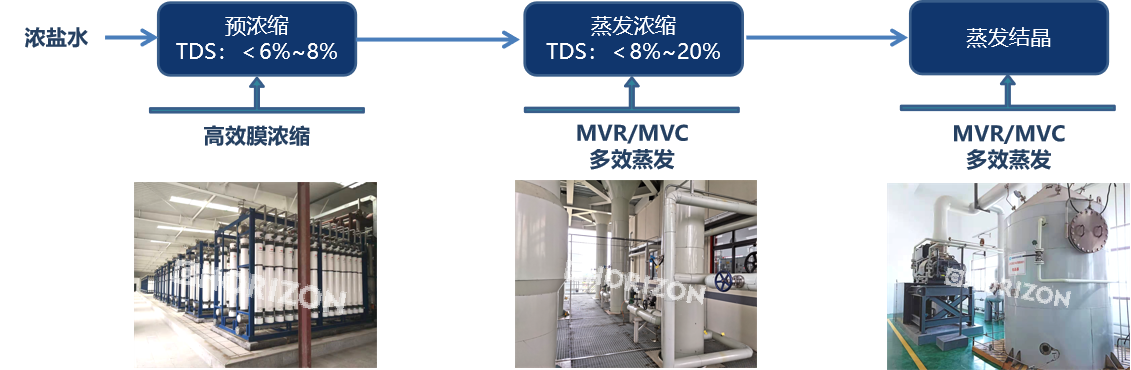
Core processes for zero discharge—evaporation and concentration, evaporation and crystallization
Evaporation and concentration: Obtaining a concentrated solution directly as a chemical product or semi-finished product; concentrating the solution to saturation for crystallization to obtain solid solute; removing impurities to obtain a pure solvent.
Evaporation and crystallization: The crystallization process is the crystallization of the solute from the solution, which involves two steps. The first is nucleation, where microscopic grains are first generated as the core of the crystal, which is called the nucleus. The second is crystal growth, where the nucleus grows into a macroscopic crystal, a process called crystal growth. Both the nucleation process and the crystal growth process are driven by the supersaturation of the solution, including primary homogeneous nucleation, primary heterogeneous nucleation, and secondary nucleation. Secondary nucleation is mainly contact nucleation, and nucleation in industrial crystallizers is mostly contact nucleation, which occurs in the presence of crystals of the substance to be crystallized in the solution.
Introduction to common evaporators
Single Effect evaporator
When a solution is evaporated in an evaporator, if the secondary steam produced is not reused, this evaporation operation is called single-effect evaporation. An evaporator using a single-effect evaporation method is called a single-effect evaporator.
Multiple-effect evaporator
Multiple evaporators are connected in series, and the secondary steam produced is passed to another evaporator with lower pressure as heating steam, so that the heating steam is used multiple times in the evaporation process.
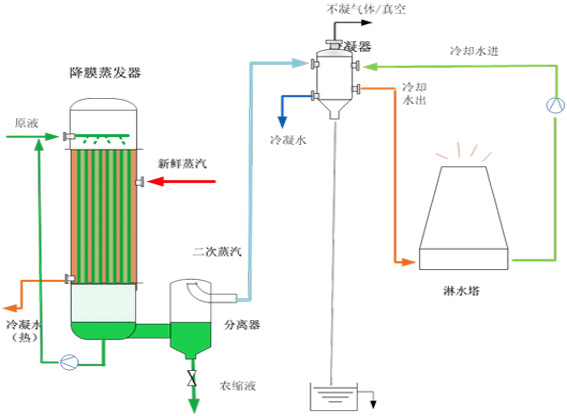
Single-effect evaporator
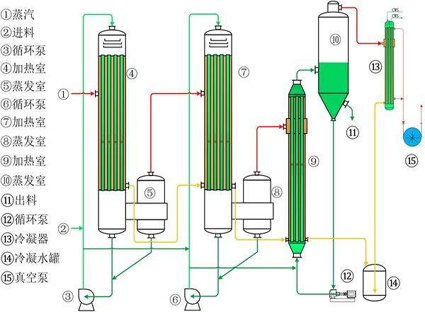
Multiple Effect evaporator
MVR evaporator
MVR is the abbreviation for Mechanical Vapor Re-compression. Its principle is to use a mechanical compressor to re-compress the secondary steam after evaporation to increase its enthalpy, which is then sent back to the heating chamber as a heat source to heat the feedstock, and its own heat release phase change becomes condensed water discharged. The heated material is evaporated and concentrated and discharged from the system as the final product. The theoretical basis of MVR is derived from Boyle's law; that is, PV/T = K (constant value)
According to this principle, when the thin secondary steam is compressed in volume, its temperature will increase and pressure will increase, thus realizing the transformation of low-temperature, low-pressure steam into high-temperature, high-pressure steam, which can then be used as a heat source to reheat the original solution to be evaporated, thus achieving the purpose of recycling and reusing steam.
Falling film evaporator
In the evaporation process, the dilute material is added from the top of the evaporator, forming a liquid film with the same direction as the steam flow, and flowing down from top to bottom. Suitable for materials with high concentration and high viscosity; not suitable for materials that are easy to crystallize.
Forced circulation evaporator
High circulation speed; can be used for evaporating materials with high viscosity and easy crystallization and scaling; high heat transfer coefficient. The heating chamber is served by a tube bundle heat exchanger, which is the heat receiving unit of the evaporation system. The heat exchange tubes are completely immersed in the solution, and the material is forced to circulate at a large flow rate between the heater and the evaporation chamber by the forced push of the circulation pump.
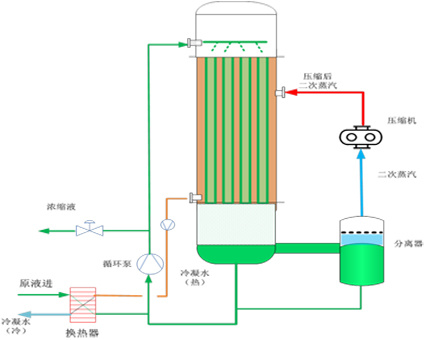
Falling film evaporator
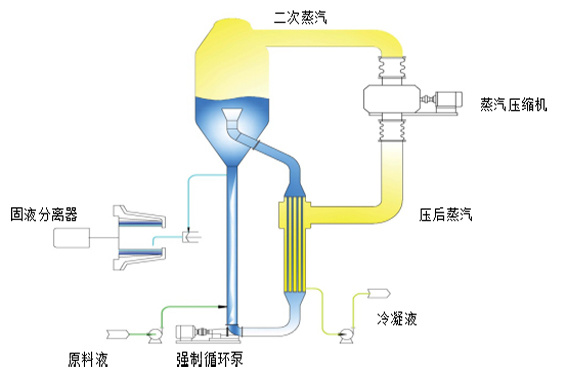
Forced circulation evaporator
Introduction to common crystallizers
Freeze crystallizer
The freeze crystallization system mainly consists of a cooler, a cooling crystallizer, and a cooling circulation pump. The cooling crystallizer is fed centrally in reverse flow, and sodium sulfate crystals settle from the top of the cooling crystallizer, ensuring sufficient residence time to ensure that the sodium sulfate crystals grow to a sufficient size. At the same time, a special overflow plate is designed in the cooling crystallizer to prevent sodium sulfate crystals from being discharged with the upper mother liquor. The mother liquor in the cooling crystallizer is reheated through a pre-heat exchanger and returned to the sodium chloride thermal crystallization system.
Melt crystallizer
According to the different freezing points of the substances to be separated, the temperature of the initial liquid mixture feed is gradually reduced to achieve partial crystallization. The crystallized solid phase has a different chemical composition from the residual liquid, thus achieving the purpose of separation and purification. In the crystallization process, as the temperature of the melt gradually decreases, a certain component is in a supersaturated state in the melt crystallization liquid, begins to nucleate, and gradually grows into crystals. In the process of crystal growth, impurities in the mother liquor are inevitably included in the crystals. The coarse crystals are purified through a sweating process.
Vacuum cooling crystallizer
The hot saturated solution is added to a crystallizer that is adiabatically insulated from the outside world. Because a high vacuum is maintained inside the crystallizer, the boiling point of the solution retained inside is lower than the temperature of the added solution. In this way, when the solution enters the crystallizer, it is cooled to the equilibrium temperature corresponding to the pressure inside the crystallizer through an adiabatic flash evaporation process.
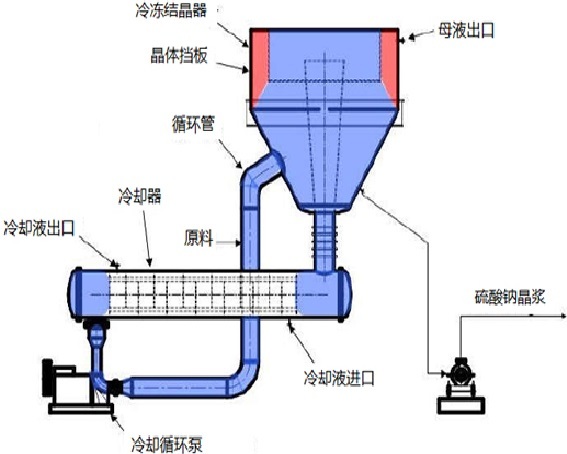
Freeze crystallizer